Streamlined and lean waste management
The amount of material handling operations that don’t provide value is reduced with a Lean approach to waste management. By increasing efficiency, lean waste management helps organizations save time, space, and money.
Ineffective methods for managing waste
In many businesses, it is customary to place tiny bins around the building to collect waste or recyclable materials like cardboard and plastic. These are shown as tiny blue dots in the image to the right.
The waste must then be gathered and brought to one or more outside containers several times per day, where it must be further sorted and processed by folding or cutting before being loaded into a container or compactor.
An interrupted and ineffective workflow is the result of this. When cargo is delivered by forklift truck (FLT), there is a larger chance of faulty sorting and a higher risk of internal mishaps.
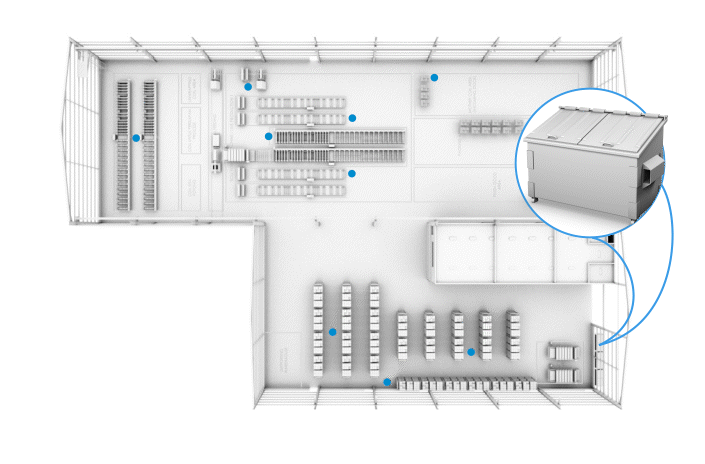
Standard outdoor waste containers come with a number of drawbacks
There are various drawbacks when businesses employ external waste containers for waste collection:
• Significant time wastage in the movement of materials to the exterior container area and additional loading time
• Uncompacted cardboard and EPS (Polystyrene) waste space, necessitating the use of additional containers or pricey collections.
• Constant collection costs: regardless of whether the container is full or not, it gets emptied.
• Wrong substance in the incorrect container! Inaccurate sorting results in extra costs.
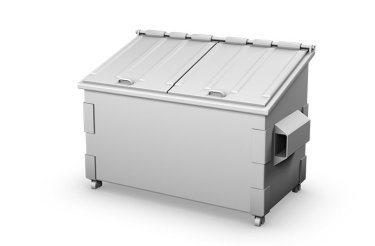
The Lean methodology focuses on optimizing operations by getting rid of extraneous steps, cutting down on visits both inside and outside the company, and making ongoing improvements.
Although lean methods are common in industrial settings, they can also be very useful in other fields.
Advantages of Lean waste management
When designing waste solutions, Mil-Tek follows lean concepts. With a Lean-based waste management strategy, our compressed air-driven waste compactors are placed as close to the unpacking area as is practical, as seen in the image to the right.
Without having to fold it or “walk with it” to a container, the waste can then be handled right away, straight in a cardboard baler or plastic baler. Up to 90% of the debris is compacted in the baler. When it signals a full bale, it is quickly and safely emptied. The compressed bales are simple to store and can be collected for recycling later.
Lean waste management produces a significantly more productive workflow, allowing you to manage garbage more efficiently while also saving money on containers and collections, as well as a significant amount of time and space.
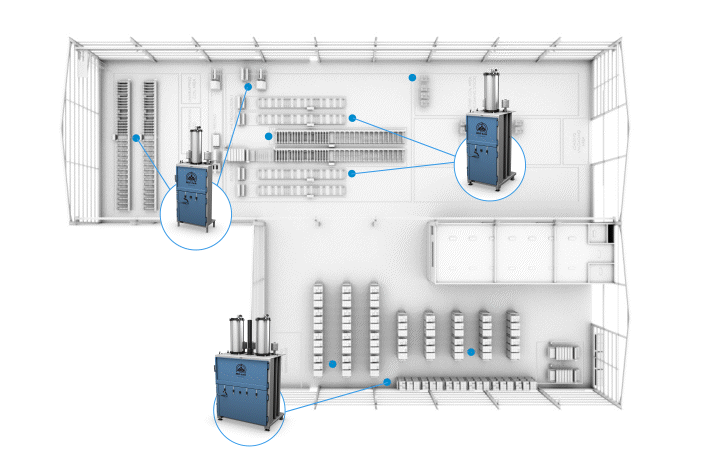
Reduce waste through lean management and forklift use
Forklift truck driving is a common source of workplace accidents, many of which have significant repercussions. When there is a mix of vehicle and pedestrian traffic, there is a higher danger of accidents, which is exacerbated by clutter in the transport area.
The requirement for forklift truck driving is drastically reduced with a lean approach to trash management, where waste is compacted at the source, leading to improved safety standards.
Reduce trips by truck by 10:1
Your excursions can move ten times as much material when the material is compressed before being transported. This many fewer journeys means fewer mishaps, greater effectiveness, and cost savings.
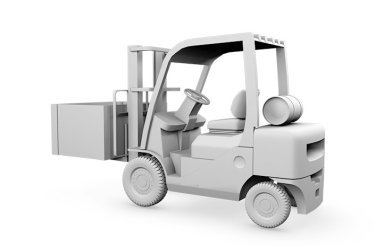
4 important Lean principles
You can learn more about the four fundamental Lean principles used by Mil-tek to tailor waste solutions for you here.
“Kaizen” also known as continuous improvements
The entire team must be involved in producing continuous improvements. ‘Kaizen boards’ are frequently employed by businesses to track the development of fresh Kaizen suggestions for increasing productivity.
“8 types of waste”
TIMWOODS! A great way to remember the 8 sources of waste: Time, Inventory, Motion, Waiting time, Overproduction Over-processing, Defects, Skills.
“Value Stream Mapping”
Mapping production flows or other processes with a view to identifying areas that can be improved or made more efficient.
“5S” – a tool for creating system and order
Sort, Set in order, Systematic cleaning, Standardize, Self-discipline. By working with 5S you can achieve: Better ergonomics, improved working environment, higher quality, time saving, increased productivity, employee well-being, etc.
– A sixth ‘S’ has now been added: Safety; All of the above are to be carried out in a safe working environment.
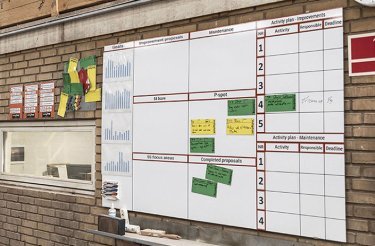
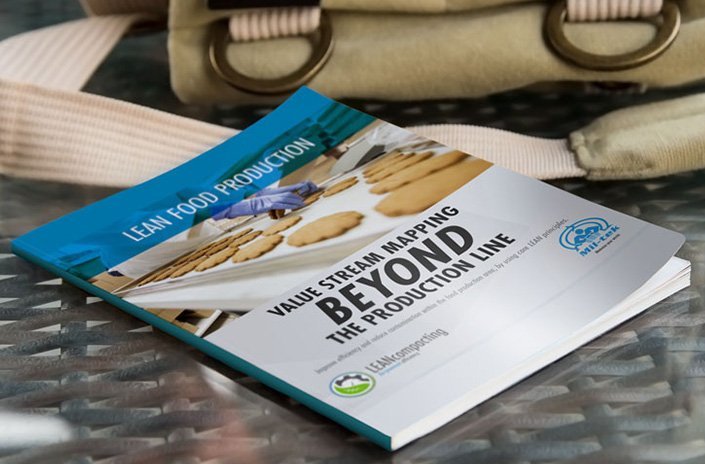
Looking to learn more about Lean?
Have you started to wonder how, after adopting a lean strategy, you may optimize waste management to reap several advantages and make significant savings?
Use this form to contact us, and we’ll get back to you right away.