HydraSpecma’s waste handling is now more Lean driven
Instead of carrying cardboard and plastic waste to external containers several times a day, staff can now concentrate solely on duties that offer value to the company.
75% decrease in forklift driving due to Lean compacting
By applying a Lean and sustainable solution to their waste management procedures, Hydra Specma was able to minimize internal truck traffic by 75% while also saving 8 man-hours per week.
0%
Deficient Lean production areas
Being a reputable Danish corporation with 300 employees, Hydra Specma supplies a range of components to industry, but focus specifically on industry, wind, and offshore.
The production areas and daily operations at Hydra are all already very Lean driven. However, the company’s operations are dispersed throughout three different buildings as a result of Hydra’s ongoing growth. So, the Lean approach has become somewhat complicated to maintain.
Employees are now forced to move waste from cages in the different buildings to the outdoor waste collecting area, which has made waste disposal rather challenging and time-consuming.
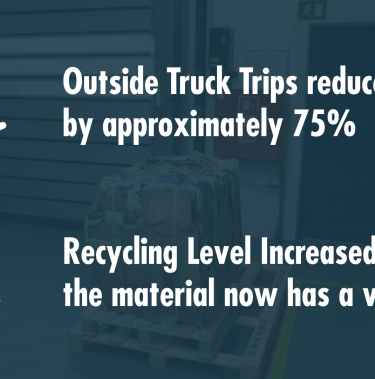
GPS value stream mapping by Mil-tek
Using GPS technology, Mil-Tek conducted a value stream mapping exercise on Hydra’s internal waste transport. It was discovered that the waste truck was leaving the production buildings on average 30 times per day and traveling 50 km each week. Additionally, it was estimated that approximately 8 hours per week were spent manually loading waste from cages into the large outdoor compactor.
Some of the waste cages were taken outside by hand, if they were closer to the outside containers, and then manually unloaded. Then returned empty to the unpacking area. Overall, the procedure was cumbersome for the staff, which Hydra also acknowledged and sought to resolve.
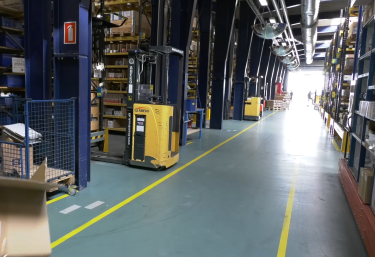
A new and better strategy
Hydra was very proactive and forward-thinking in regards to finding a better strategy. They were eager to find a solution that would prevent all the time-consuming waste-excursions outside.
Instead of the conventional waste cages around the facility, they sought a way to create localized waste zones. Additionally, they were very interested in enhancing their environmental performance and ensuring that the greatest amount of waste was recycled.
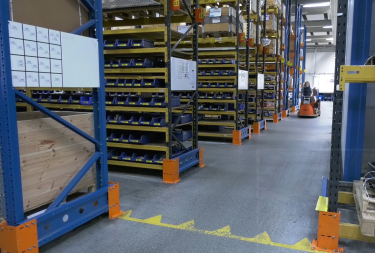
Very easy to use
Since the value stream mapping exercise, Mil-Tek has offered a range of solutions that meet Hydra’s needs and goals.
Electrical Mil-tek balers have been installed in 2 out of 3 production areas to manage heavy cardboard waste streams.
Now, employees in these areas only need to fill the balers continuously as well as bale out 1 or 2 times pr week. Because the Mil-tek solutions are very easy to use, any member of the staff can load and empty them.
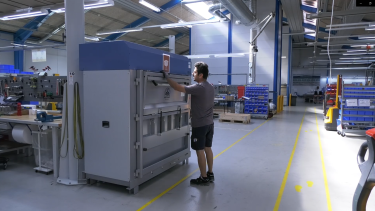
No needless waste walks
A variety of air-powered Mil-tek balers have been installed in the unpacking area and are currently managing all the cardboard and plastic waste produced when unpacking goods arrive from sub-suppliers.
All unpacking stations have an air-powered Mil-tek baler installed and also a bag stand for plastic waste. This prevents staff members from having to needlessly escort packaging waste around the facility. They can instead concentrate solely on tasks that provide value to the company.
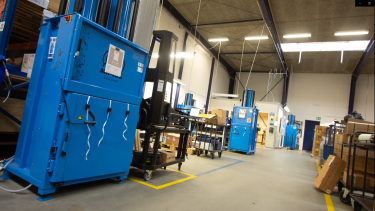
Any questions?
To discover more about how Mil-tek can help your company handle your waste more effectively – use the form to contact us.
We’ll help you save important resources like costs, time, and space.